inductive position sensor
- time:2024-11-07 11:41:23
- Click:0
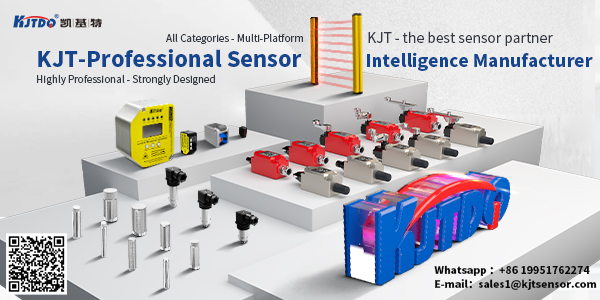
Understanding Inductive Position Sensors: A Comprehensive Guide
In the realm of sensor technology, inductive position sensors stand out as a versatile and reliable solution for various industrial applications. These devices, which rely on electromagnetic fields to detect position, play a crucial role in modern automation systems. This article aims to provide an in-depth overview of inductive position sensors, exploring their working principles, advantages, common applications, and key considerations for selection and maintenance.
How Inductive Position Sensors Work
At its core, an inductive position sensor operates based on the principles of electromagnetism. These sensors consist of a transmitter coil, which generates an electromagnetic field, and a receiver coil that detects changes in this field. When a conductive material, such as a metal target, moves within the vicinity of these coils, it alters the magnetic field, causing a change in voltage or current at the receiver coil. This variation is then processed by electronic circuitry to determine the precise position of the target.
Advantages of Inductive Position Sensors
- High Accuracy and Resolution: Modern inductive position sensors offer exceptional accuracy and fine resolution, making them suitable for even the most demanding applications. They can measure positions with sub-micron precision, ensuring reliable performance across various industries.
- Non-Contact Measurement: Unlike some other types of position sensing technologies that require physical contact, inductive sensors operate without touching the target object. This non-contact nature reduces wear and tear, extends sensor lifespan, and minimizes the risk of contamination or damage to delicate components.
- Resistance to Harsh Environments: Inductive sensors are inherently robust and resistant to extreme temperatures, humidity, dust, and even certain levels of water ingress. This durability makes them ideal for outdoor use or harsh industrial environments where other sensors might fail.
- Versatility and Flexibility: With a wide range of design options available, including different sizes, shapes, and configurations, inductive position sensors can be tailored to fit specific requirements. They can also interface easily with most control systems and digital networks, enhancing integration into existing automation setups.
Common Applications
The versatility of inductive position sensors translates into widespread adoption across numerous industries and applications:
- Automotive Manufacturing: In automotive production lines, these sensors monitor piston movement, valve positions, and gear shift mechanisms, ensuring smooth operation and safety.
- Machine Tools & CNC Machines: Precision machining relies heavily on accurate position feedback. Inductive sensors help maintain tool alignment and control during cutting processes.
- Robotics: In robotic arms and automation equipment, they facilitate precise control over joint movements and end-effector placement, enabling complex manipulation tasks.
- Aerospace & Aviation: For aircraft control surfaces and landing gear systems, inductive sensors ensure safe and responsive operation under stringent conditions.
- Hydraulics & Pneumatics: They track cylinder rod positions in hydraulic and pneumatic actuators, optimizing system performance and efficiency.
Considerations for Selection and Maintenance
Choosing the right inductive position sensor involves several factors:
- Range and Resolution: Assess the required measurement range and the necessary level of precision for your application to select a compatible sensor.
- Environmental Compatibility: Consider the operating environment, including temperature, humidity, vibration, and potential exposure to chemicals or water, to ensure sensor durability.
- Mounting Options: Depending on the space constraints and installation requirements, choose between through-bore, surface mount, or integral designs.
- Output Signal: Match the sensor’s output type (analog or digital) with your control system specifications for seamless integration.
Maintenance is relatively minimal for inductive position sensors due to their non-contact operation and robustness. However, regular checks for dirt accumulation, wiring integrity, and software updates can prolong sensor life and maintain optimal performance.
Conclusion
Inductive position sensors represent a sophisticated yet practical solution for precise motion control and monitoring in a multitude of industries. Their ability to deliver high accuracy, resist harsh environments, and adapt to diverse applications make them a cornerstone of modern automation technology. By carefully considering application needs and selecting the appropriate sensor model, engineers can leverage inductive position sensors to enhance system reliability, improve productivity, and drive innovation forward.