high temperature pressure transducer
- time:2024-10-22 02:02:49
- Click:0
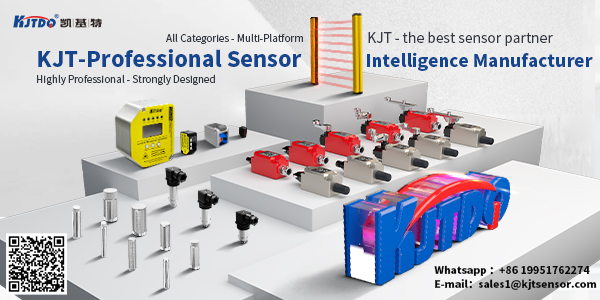
High-Temperature Pressure Transducers: Innovations and Applications in Monitoring Extreme Conditions”
In the realm of industrial technology, monitoring pressure and temperature within extreme environments is crucial for ensuring safety, efficiency, and accuracy. High-temperature pressure transducers have emerged as indispensable tools in a variety of industries that operate under intense conditions, providing critical measurements necessary for control systems and data acquisition processes. This article delves into the innovations behind high-temperature pressure transducers, their applications, and the benefits they bring to modern industry.
Understanding High-Temperature Pressure Transducers
At their core, high-temperature pressure transducers are devices designed to measure pressure in environments where temperatures exceed the capabilities of standard pressure sensors. Typically made from heat-resistant materials like stainless steel or ceramics, these transducers can withstand continuous exposure to high temperatures without degradation in performance or longevity. They are engineered to provide accurate pressure readings even when subjected to thermal cycling and extreme thermal gradients.
Technological Innovations Shaping the Future
One of the significant advancements in high-temperature pressure transducer technology is the development of solid-state sensors. Unlike traditional sensors that rely on liquid-filled systems, solid-state sensors offer improved stability and faster response times. They are less prone to failure under harsh conditions, ensuring reliable performance in challenging applications.
Another innovation is the integration of wireless technology into high-temperature pressure transducers. This allows for remote monitoring and data transmission without the need for extensive wiring, reducing installation complexities and enhancing system flexibility. Wireless sensors are particularly beneficial in hard-to-reach areas or moving machinery where wire routing is impractical.
Applications Across Industries
The use of high-temperature pressure transducers spans across numerous sectors, each with its unique set of challenges and requirements:
- Oil and Gas Industry: In drilling operations, downhole pressure and temperature measurement are vital for managing well productivity and avoiding blowouts. High-temperature pressure transducers are deployed to monitor these parameters accurately, ensuring safe extraction processes.
- Aerospace and Aviation: Engine health monitoring in jet engines relies on high-temperature pressure transducers to measure turbine blade stresses and combustion chamber pressures, enabling preventative maintenance and enhancing flight safety.
- Automotive Sector: Modern internal combustion engines and turbochargers operate at higher efficiencies and temperatures than ever before. High-temperature pressure transducers play a key role in engine management systems, optimizing performance while ensuring emissions compliance.
- Power Generation: In power plants, especially those using fossil fuels or nuclear energy, precise pressure and temperature monitoring is essential for efficient operation and safety. High-temperature pressure transducers help control steam cycles and prevent equipment failures.
- Petrochemical Plants: Chemical reactions often occur at elevated temperatures and pressures; hence, high-temperature pressure transducers are employed to ensure process safety, optimize yields, and maintain product quality.
Benefits of High-Temperature Pressure Transducers
Investment in high-temperature pressure transducers offers several advantages for industrial operations:
- Enhanced Safety: Accurate pressure monitoring helps detect potential hazards early, allowing timely interventions that prevent accidents.
- Operational Efficiency: By providing precise data, these transducers enable better control over processes, improving overall efficiency and reducing energy consumption.
- Cost Savings: Reliable measurements lead to optimized process conditions, reducing waste and maintenance costs associated with equipment failures.
- Compliance and Quality Control: Meeting industry standards and regulatory requirements becomes easier with accurate monitoring, ensuring products meet quality benchmarks consistently.
Conclusion
High-temperature pressure transducers represent a leap forward in the ability to manage extreme industrial environments safely and efficiently. As technologies continue to evolve, so too will their applications, pushing boundaries in various fields from oil extraction to aerospace engineering. Embracing these innovations not only drives progress but also fortifies the very foundations upon which modern industry stands.