laser displacement transducer
- time:2024-10-19 01:24:20
- Click:0
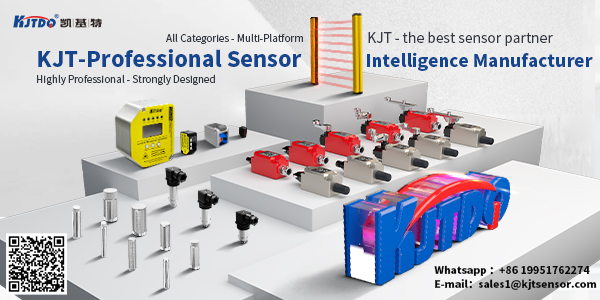
Laser Displacement Transducer: A Comprehensive Overview
A laser displacement transducer is a crucial instrument in various industries, providing precise measurements of the distance between two points. This device utilizes laser technology to measure the displacement of an object with high accuracy and reliability. In this article, we will explore the working principle, applications, advantages, and limitations of laser displacement transducers.
Working Principle
A laser displacement transducer works on the principle of reflection of light. It emits a beam of laser light towards the target object, and when the light hits the surface, it gets reflected back to the sensor. The time taken by the light to travel from the sensor to the target and back is measured, which is then used to calculate the distance between the two points. The main components of a laser displacement transducer include a laser diode, a lens, a photodetector, and a microprocessor.
Applications
Laser displacement transducers have a wide range of applications across various industries due to their precision and reliability. Some of the prominent applications include:
- Machine Tool Alignment: Laser displacement transducers are extensively used in machine tool alignment to ensure accurate positioning and alignment of tools and parts.
- Vibration Analysis: These transducers are used to measure vibrations in rotating machinery, such as turbines, motors, and pumps, to monitor their health and performance.
- Thickness Measurement: Laser displacement transducers are employed in measuring the thickness of materials, such as metal sheets, glass panels, and plastic films, with high precision.
- Automotive Industry: In the automotive industry, these transducers are used for various applications, such as measuring tire tread depth, detecting wheel speed, and monitoring engine vibrations.
Advantages
Laser displacement transducers offer several advantages over traditional measurement techniques, making them the preferred choice for many industrial applications. Some of the key advantages include:
- Non-Contact Measurement: Laser displacement transducers provide non-contact measurement, eliminating the risk of damage to delicate or sensitive surfaces.
- High Precision: These transducers offer high precision and accuracy in measurements, making them suitable for critical applications where even minor errors can have significant consequences.
- Fast Response Time: Laser displacement transducers have a fast response time, enabling real-time monitoring and measurement of dynamic systems.
- Wide Range of Applications: These transducers are versatile and can be used in various industries and applications, as discussed earlier.
Limitations
Despite their numerous advantages, laser displacement transducers also have some limitations that need to be considered while selecting the appropriate measurement technique for a specific application. Some of the limitations include:
- Environmental Sensitivity: Laser displacement transducers are sensitive to environmental factors such as temperature, humidity, and vibrations, which can affect their accuracy and reliability.
- Line-of-Sight Issues: These transducers require a direct line-of-sight between the sensor and the target object, which might not always be possible in certain applications or environments.
- Cost: Laser displacement transducers can be expensive compared to other measurement techniques, which might be a limiting factor for some industries or applications.
In conclusion, laser displacement transducers are powerful and versatile instruments that offer high precision and accuracy in measurements across various industries. However, it is essential to consider their limitations and select the appropriate measurement technique based on the specific requirements of the application.