inductive proximity sensor sensing range
- time:2024-10-15 00:42:18
- Click:0
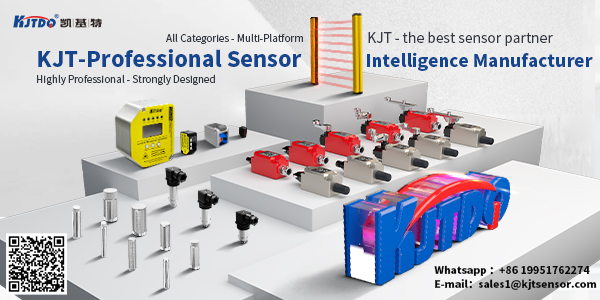
Title: The Importance of Inductive Proximity Sensor Sensing Range
In today’s world, sensors play a crucial role in our daily lives. They are used in various applications, from industrial automation to healthcare. One type of sensor that has gained significant importance is the inductive proximity sensor. This sensor is widely used due to its ability to detect the presence of metal objects without any physical contact. However, one of the most critical specifications of an inductive proximity sensor is its sensing range. In this article, we will discuss the significance of the inductive proximity sensor sensing range and how it affects its performance.
- What is Inductive Proximity Sensor Sensing Range?
The sensing range of an inductive proximity sensor refers to the maximum distance between the sensor and the metallic object it can detect. It is typically measured in millimeters (mm). The sensing range depends on several factors, including the size and shape of the target object, its material properties, and the environmental conditions surrounding the sensor.
- Importance of Sensing Range
The sensing range of an inductive proximity sensor is essential because it determines how effectively the sensor can detect the presence of a metallic object. A larger sensing range allows the sensor to detect objects from a greater distance, which is beneficial in applications where space is limited or when detecting large objects. On the other hand, a smaller sensing range may be more suitable for applications where precision is crucial, such as in medical devices or aerospace components.
- Factors Affecting Sensing Range
As mentioned earlier, the sensing range of an inductive proximity sensor depends on several factors. One of the most significant factors is the size and shape of the target object. Larger objects with flat surfaces tend to have a longer sensing range than smaller objects with curved surfaces. Additionally, the material properties of the target object, such as permeability and conductivity, can also affect the sensing range. For example, non-magnetic materials like copper and aluminum have a shorter sensing range compared to magnetic materials like iron and steel.
- Environmental Conditions
The environment in which an inductive proximity sensor operates can also impact its sensing range. Factors such as temperature, humidity, and electromagnetic interference can cause fluctuations in the sensor’s performance. Therefore, it is essential to choose a sensor that is designed to operate under specific environmental conditions to ensure accurate and reliable detection.
- Applications of Inductive Proximity Sensors
Inductive proximity sensors are used in various applications across different industries due to their reliability and versatility. Some common applications include:
a) Industrial Automation: Induction sensors are widely used in conveyor belts, packaging machinery, and robotic arms to detect the presence of metal parts and control processes accordingly.
b) Automotive Industry: Induction sensors are used in car doors, airbags, and seat belts to detect when a metal object is nearby and activate safety features.
c) Medical Devices: Induction sensors are used in medical equipment like MRI machines and pacemakers to detect the presence of metal implants and monitor patient vital signs.
- Conclusion
In conclusion, the inductive proximity sensor sensing range is a critical parameter that determines its effectiveness in detecting metallic objects. It is essential to choose a sensor with an appropriate sensing range based on the application requirements and environmental conditions. With advancements in technology, induction sensors continue to evolve, providing more accurate and reliable detection capabilities for various industries.