Title: The Magic of Magnetic Inductive Sensors
- time:2024-10-12 13:58:46
- Click:0
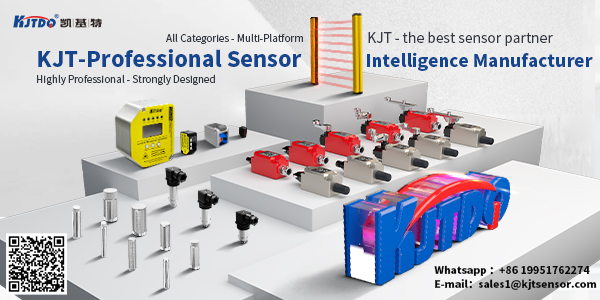
Introduction:
Magnetic inductive sensors, also known as MIS, are a type of proximity sensor that use electromagnetic fields to detect the presence of metal objects. They have become increasingly popular in various industries due to their high accuracy, reliability, and versatility. In this article, we will explore how magnetic inductive sensors work, their applications, advantages, and potential future developments.
How do Magnetic Inductive Sensors Work?
Magnetic inductive sensors consist of two main components: a coil and a magnet control. The coil is wound around a ferrite core, and when an alternating current passes through it, it generates a magnetic field. This magnetic field interacts with the magnetic material near the sensor, causing eddy currents to flow within the material. These eddy currents produce a secondary magnetic field that opposes the original one. As a result, the induced voltage in the coil changes depending on the distance between the sensor and the target material. By measuring this change in voltage, the sensor can determine the position or movement of the target object.
Applications of Magnetic Inductive Sensors:
Magnetic inductive sensors have a wide range of applications across different sectors. Some common examples include:
- Automotive industry: MIS are used in anti-lock braking systems (ABS), engine management systems, airbags, seat belts, door locks, and mirror adjustments. They help improve safety and comfort by detecting metal parts’ position or movement accurately.
- Machinery and equipment manufacturing: MIS are used in conveyor belts, packaging machines, robotic arms, printing presses, textile machinery, and food processing lines. They ensure precise control over mechanical operations and improve efficiency.
- Medical devices: MIS are used in surgical instruments, prosthetic limbs, dental equipment, hearing aids, and diagnostic imaging machines. They provide accurate measurements of biological tissues or metal implants without invasive procedures.
- Aerospace and defense: MIS are used in aircraft landing gear systems, missile guidance systems, perimeter security systems, and weapon control systems. They offer high reliability and performance under extreme operating conditions.
Advantages of Magnetic Inductive Sensors:
- Non-contact detection: Unlike mechanical switches or optical sensors that require physical contact with the target object, MIS operate at a distance and do not wear out over time. This makes them ideal for harsh environments where contamination or damage may be an issue.
- High precision and repeatability: MIS provide consistent results regardless of environmental factors such as temperature or humidity. They can measure small movements or vibrations with sub-millimeter accuracy.
- Wide detection range: MIS can detect metallic objects from a few millimeters to several centimeters away depending on their design and application requirements. This makes them suitable for various industrial processes and automation systems.
Potential Future Developments:
As technology advances, there are several potential areas where magnetic inductive sensors could evolve further:
- Miniaturization: Reducing the size of MIS would enable their integration into smaller devices such as wearable electronics or medical implants. It could also expand their application possibilities in consumer electronics and smart homes.
- Integration with Internet of Things (IoT): Combining MIS with IoT platforms would allow real-time monitoring and analysis of data collected by the sensors. This could lead to more efficient process optimization, predictive maintenance, and enhanced safety features in industrial settings.
- Energy harvesting: Exploiting the energy generated by eddy currents induced in metal targets could power wireless sensor networks or low-power devices without external power supplies. This would reduce maintenance costs and extend the lifespan of battery-powered systems.
Conclusion:
Magnetic inductive sensors have come a long way since their introduction and have found numerous applications across various industries. Their unique non-contact detection capability, high precision, and wide detection range make them indispensable tools for modern automation systems. With ongoing research and development efforts focusing on miniaturization, IoT integration, and energy harvesting, we can expect even more innovative uses for these fascinating sensors in the future.